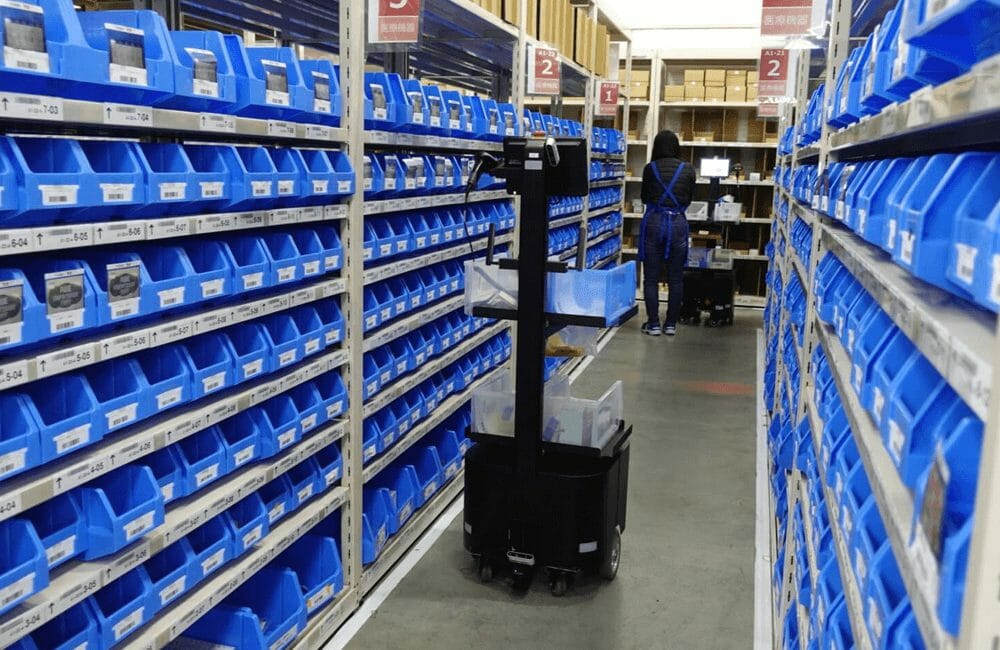
物流業界は人手不足が慢性化しています。その状況を改善するためにここ数年で物流ロボットの導入が急速に進んでいます。
数ある物流ロボットの中でも今回はAMR(協働搬送ロボット)を取り上げて、
AMRの概要、導入メリット、その他ロボットとの比較について解説いたします。
AMRには多くのメリットが存在します。
- ピッキング業務の生産性が従来の2倍に向上する
- 既存ラックのレイアウト変更が必要なく、業務を止めることなく導入が可能
- 他のロボットと比較して導入コストが小さい
本記事を最後まで読んでいただければ、AMRの特徴や導入メリットについて理解することができます。
Contents
AMR(協働搬送ロボット)とは?
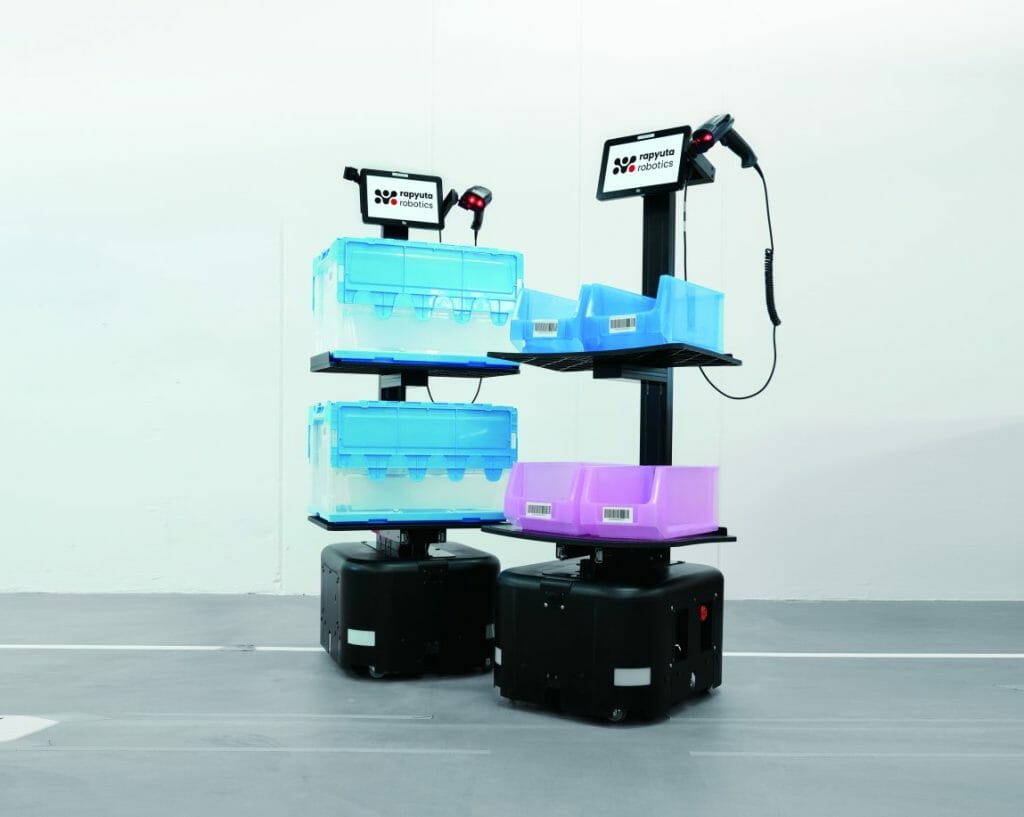
AMR(Autonomous Mobile Robot:自立走行搬送ロボット)は、作業者と協調しながら活躍するピッキング支援ロボットです。
ロボットに搭載されたセンサー、AIにより自律走行が可能で、作業者や障害物を回避しながら目的の場所まで移動し、ピッキング作業を補助します。
作業者がピッキングした荷物を運搬したり、ピッキングのロケーションに先行して移動し場所を知らせるなど、従来作業者が行っていた作業を代わりに行い、生産性の向上に貢献します。
AMRを提供する代表的なメーカー4社
ラピュタロボティクス(rapyuta robotics)
2014年に設立された会社で、エンジニアリング部門をスイス、本社を東京に置きスタート。2019年から物流事業に参入し、ピッキングアシストロボット「PA-AMR」を開発しました。
2022年には生産性の向上度合に応じて料金が変動する「費用対効果保証プログラム」の提供をスタートし、AMRの導入障壁を下げる試みも行っています。
シリウス(Syrius、炬星)
2019年に設立された中国系企業で、物流ロボット「FlexComet」やAIoTサービスを提供しています。Raas(Robotics as a Service)方式で従量課⾦するサブスクリプションモデルを提供しており、ランニングコストの最適化を実現できます。
グラウンド(GROUND Inc.)
2015年に設立された日本企業で、AIを活用した物流施設統合管理・最適化システム「GWES」をはじめとした統合管理・最適化システムなど、物流全体の最適化を実現する各種ソリューションを提供しています。
寺岡精工(テラオカ)
1925年に創業した老舗の日本企業で、POSレジやはかり、ラベルプリンターなど流通小売や食品製造、物流に関わる領域で様々な製品を開発しています。
テラオカ社のAMR(AIピッキングカート)には高精度の計量器が搭載されており、商品間違いや数量の誤投入といったピッキングミスを防止する機能が搭載されているのが特徴です。
AMRとAGVの違いは?
AMRとAGVの違いについてご存知でしょうか?
(一社)日本産業車両協会によると、AGV(Automatic Guided Vehicle:無人搬送)は「一定の領域において、自動で走行し、荷など人以外の物品の搬送を行う機能を持つ車両」とあり、AGVは無人で走行する車両全般を指した用語と定義されています。
無人搬送車(AGV)の定義
一般社団法人 日本産業車両協会 「無人搬送車の種類」より引用
無人搬送車とは、一定の領域において、自動で走行し、荷など人以外の物品の搬送を行う機能を持つ車両で、道路運送法に定められた道路では使用しないもの
http://www.jiva.or.jp/pdf/Kind%20of%20AGVS.pdf
しかし、物流ロボットの種類の増加や技術の発展による誘導方式の多様化により、AMRとAGVの定義はメーカー各社によって異なり、区別が曖昧になっているのが実情でもあります。
本記事では「AMR=人と協働するピースピッキング支援ロボット」、「AGV=棚搬送ロボット(GTP)」として説明いたします。
AMRと他の物流ロボットとの比較。安価でクイックに導入できるAMRは生産性向上の効果的なソリューションに
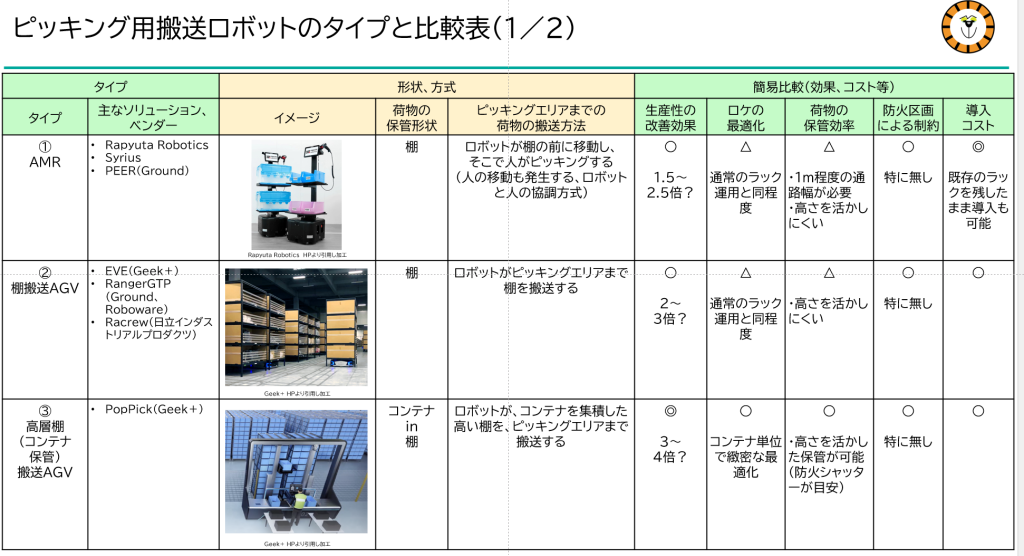
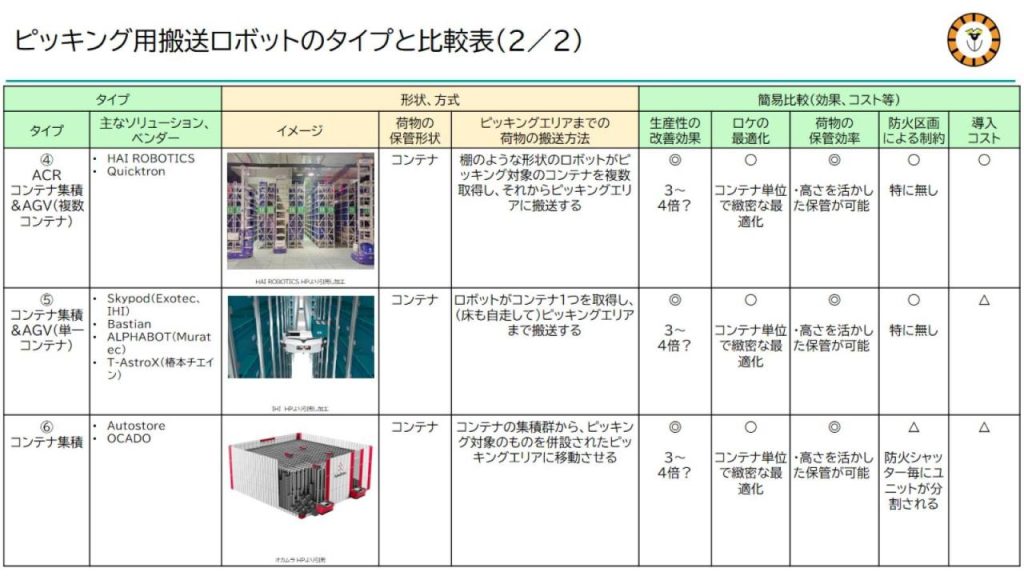
他の物流ロボットと比較してもAMRは下記のメリットがあります。
- 導入時のレイアウト変更の必要がなく、導入が比較的容易
- 導入費用が数百万~数千万規模と他の物流ロボットよりも安価に導入が可能
- 150坪規模の倉庫から導入可能
- 最短4ヶ月で導入が可能なスピード感
他の物流ロボットと比較すると生産性の向上度合いは劣りますが、既存設備のレイアウトを維持したままの導入が可能であることや、費用面での優位性から
スチールラック運用の倉庫において、AMRは生産性を上げるためのソリューションのひとつとなります。
AMRを導入するメリット
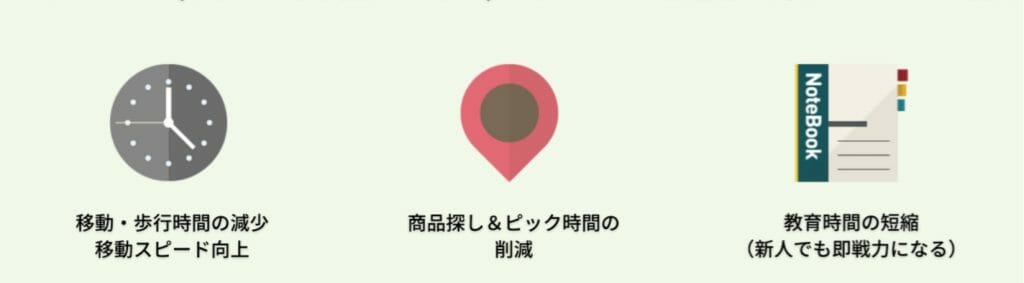
AMR(ピッキング支援ロボット)を導入するメリットは数多くありますが、主なメリットとして次の3つがあげられます。
移動(歩行)時間の削減 & 移動スピード向上
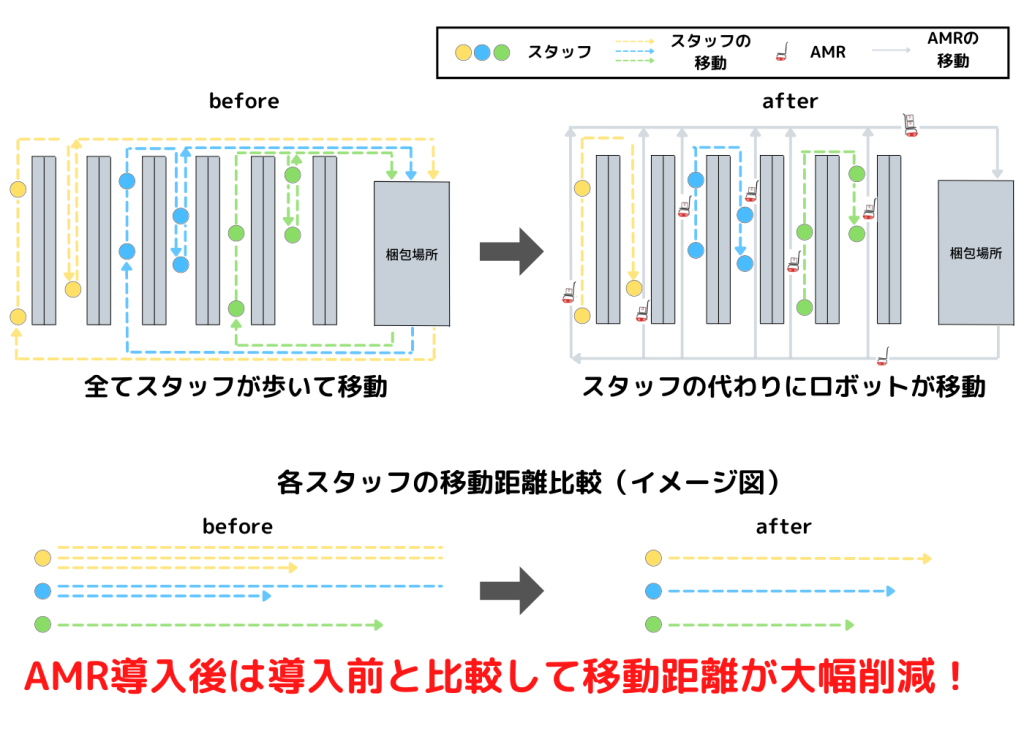
AMRを導入することの最大のメリットとして、「移動(歩行)時間の削減&移動スピード向上」があげられます。
ピッキング作業のうち、半分以上の時間は移動時間(歩行時間)で占められています。
AMRの導入によって移動時間、移動距離が大幅に削減されることによってピッキング作業に充てる時間が増加し、生産性が向上します。
荷物の運搬もAMRが行うのでスタッフは手押し台車を押して移動する必要が無くなり、負担の軽減と移動スピードの向上も見込めます。
商品探し&ピック時間の削減

業界を問わず少量多品種の流れは加速しており、倉庫で管理するSKU数は年々右肩上がりで増え続けています。
SKU数の増加に比例して、ロケーションまで移動→指定の棚内での商品探し→注文伝票(納品書)と照合する、という一連のピッキング作業にかかる時間も膨大になるという課題を抱えています。
AMRは注文データからピッキングの最短経路を算出し、ピッキング場所に先回りしてピッキング商品を指示します。
スタッフはピッキングに専念することができるようになり、生産性の大幅向上が実現可能です。
教育時間の短縮、教育コストの削減

AMR導入後はロボットのピッキング指示に従うだけでピッキング作業を進められるので、
新しいスタッフでもすぐに効率よく作業が可能となり、教育時間の短縮、教育コストの削減が実現できます。
派遣、パート人材を効率良く稼働させる事が可能になり、フレキシブルに人員を増減させることで波動対応も容易になります。
AMR導入による物流改善事例、すでに生産性が2倍に向上したケースも
AMRを導入した事業者様は年々増加していますが、すでに成果が上がっている現場も出てきています。
2020年頃から導入事例が発生しており、年々導入する事業者も右肩上がりで増加しております。
労働者人口の減少とそれに伴う雇用単価の上昇により、慢性的な人手不足の問題は今後も続いていくことが想定される以上、ロボットやAIを活用した物流改善は物流事業者によって重要な課題となります。
導入事例:佐川グローバルロジスティクス株式会社
物流最大手の佐川グローバルロジスティクス様では、AMRを導入後半年で生産性が以前の2倍までアップした実績が上がっています。
佐川グローバルロジスティクス株式会社
https://www.rapyuta-robotics.com/ja/use-cases/case-sgl/
業種:3PL(BtoB向け商材)
スタッフ数:11名/日
AMR導入台数:11台
AMR稼働日:2020年8月~
導入形態:サブスクリプション(月額利用型)
佐川グローバルロジスティクス 柏SRC(ラピュタロボティクス)
Q. AMRを運用する中で、実際に結果としてどのような成果が出てきていますか?
https://www.rapyuta-robotics.com/ja/use-cases/case-sgl/
「実態として、時間あたりの処理量が凄まじくあがっています。例えばシステムトラブルなどで、今日はロボットが動かせないという日があると、進捗が全然違います。たった1~2時間でも明らかに影響が大きいなと感じますね。『すぐに2~3個の出荷を処理したい』みたいな瞬発力を要する出荷作業だと、人間がハンディをもって処理するほうがいいのですが、1日通しての作業を時間あたりで見ていくと、まったく違います。AMRが止まったとたん、進捗が目に見えて悪くなるのは実感するようになりました。
数字でいえば、導入前後の生産性だけの比較では、現状ですでに2倍には到達していますね。処理量としては、ハンディのみの時と、AMR導入後での大きく違いがでてきています」
佐川グローバルロジスティクス 柏SRC(ラピュタロボティクス)
AMRはどうやって動く?デモ映像を通じてロボットとヒトが協調する現場を体感する
ここまででAMRの仕様や特性、導入メリットはご理解いただけたかと思いますが、次にAMRが実際に現場でどのように動き、ピッキング作業を行うかを動画、画像にて紹介いたします。
ⅰ. ピッキング作業の流れ
次に、動画の内容に沿ってピッキング作業における各工程の作業内容、従来の作業と比較した場合のメリットについて解説いたします。
ⅰ-1.WMSからのオーダーデータを適切な機体に割り当てし、ルート算出を行う(2:06~)
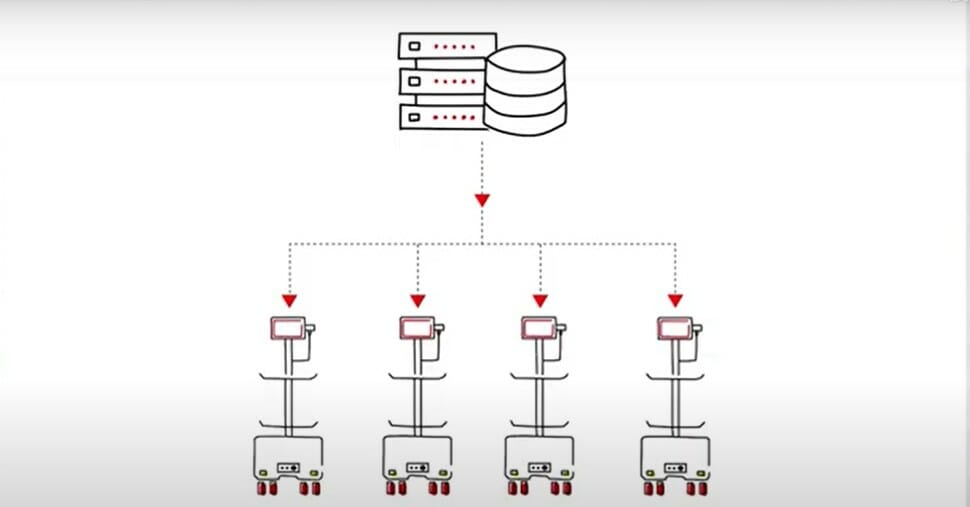
WMSからのオーダーデータをAIが処理し、最短経路でピッキングできるよう各機体にデータが割り当てされます。

ⅰ-2.オーダーが割り当てられたAMRにコンテナを載せる(2:21~)
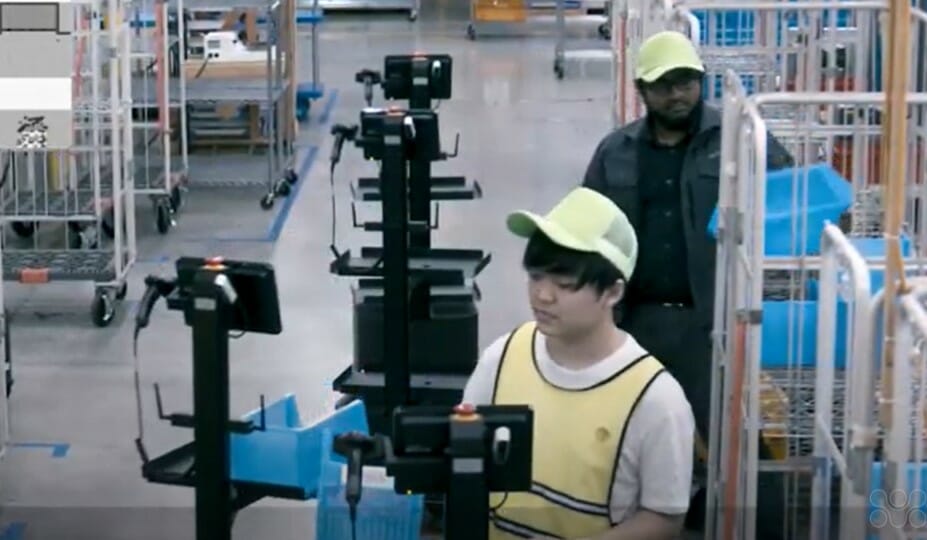
オーダーが割り当てられたAMRがコンテナ積載場所まで移動するので、スタッフはAMRにコンテナを載せます。

ⅰ-3.モニターで自分が担当するAMRを確認し、AMRが指定した位置まで移動する(2:47~)
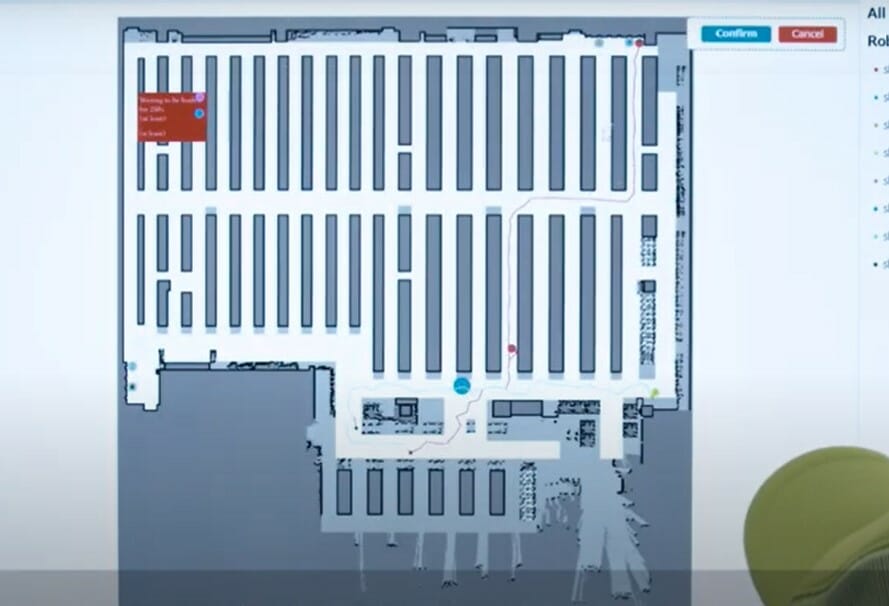
スタッフは倉庫内マップとAMRの位置が表示されたモニターを確認し、自分が担当するAMRを確認することができます。各スタッフは自分の担当するAMRが指示する場所に移動し、ピッキングを開始します。

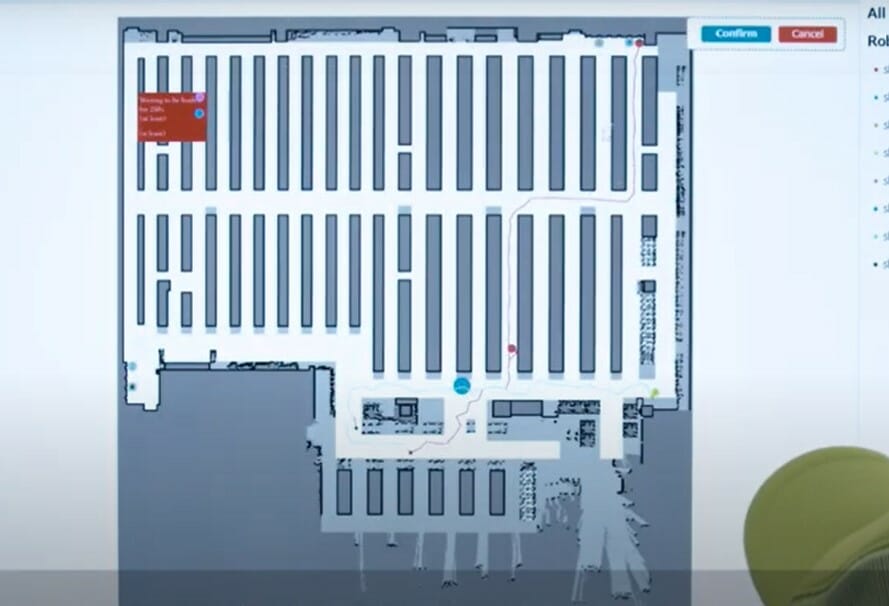
ⅰ-4.AMRが指定した位置まで移動し、表示される指示に従いピッキング(3:09~)
スタッフはAMRが指定した位置まで移動後、モニターに表示される商品をピッキングし指定のコンテナに投入します。

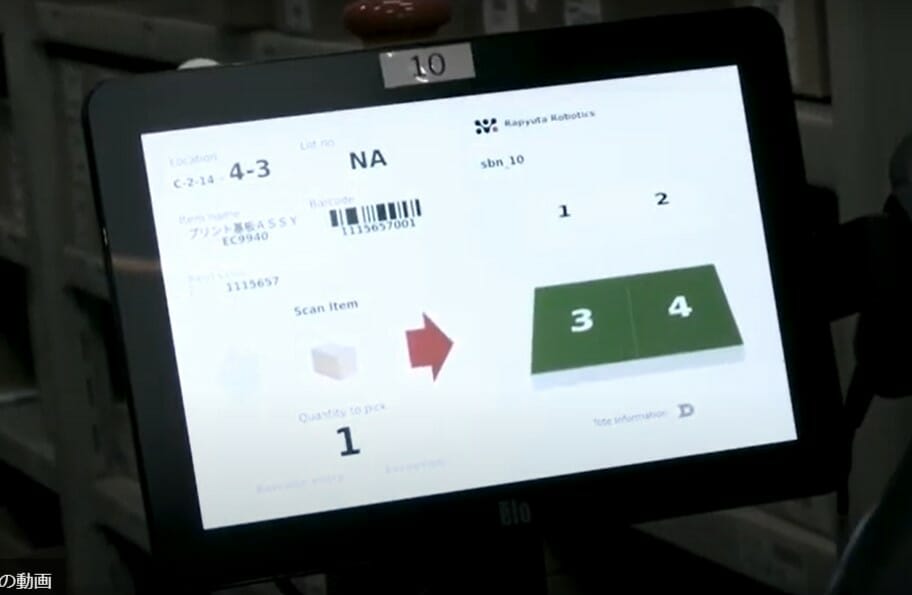
ⅰ-5.ピッキング終了後、「完了」ボタンを押すと次の場所が指示されるので移動(3:20~)
ピッキング作業終了後、モニターに表示される「完了」ボタンを押すと次のピッキング場所が表示されるので、スタッフは指定の場所まで移動します。
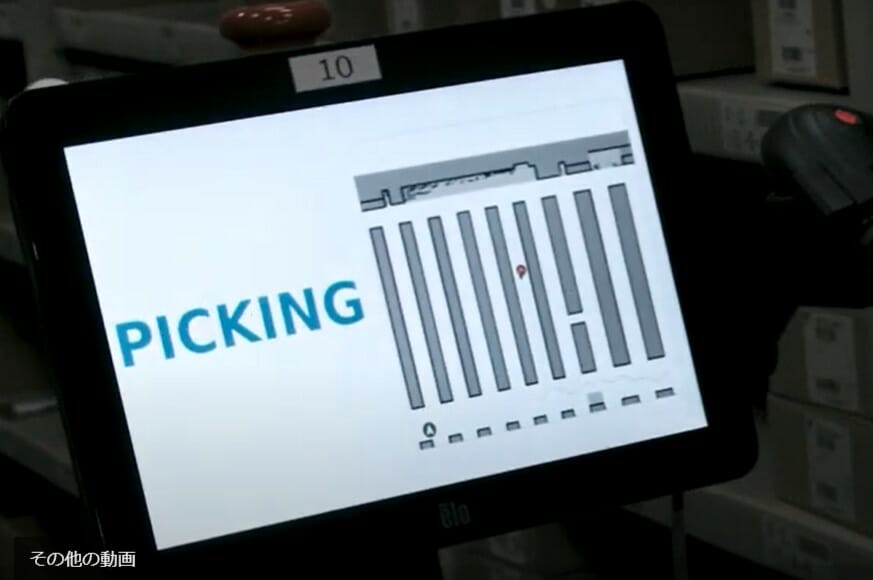
ⅱ.その他の機能について
AMRには安全に運行するための機能が搭載されています。
ⅱ-1.緊急停止スイッチや障害物センサーを搭載し、安全な走行を実現
AMRはスタッフやラック等の障害物との接触を防止するための緊急停止スイッチや障害物センサーが搭載されています。スタッフが長時間AMRの移動ルートを塞いでしまった場合は、迂回ルートを算出し目的地まで移動を行います。
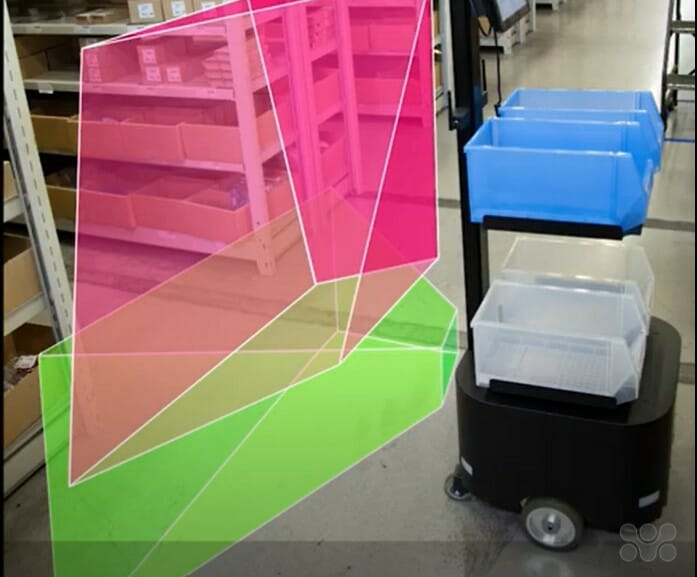
ⅱ-2.混雑度合いに応じて、移動速度を自動調整
AMRは倉庫内の混雑度合いにより走行速度を自動調整します。混雑時にはスタッフや他のAMRとの接触が発生しないよう低速で動き、混雑していない場合は高速で稼働します。
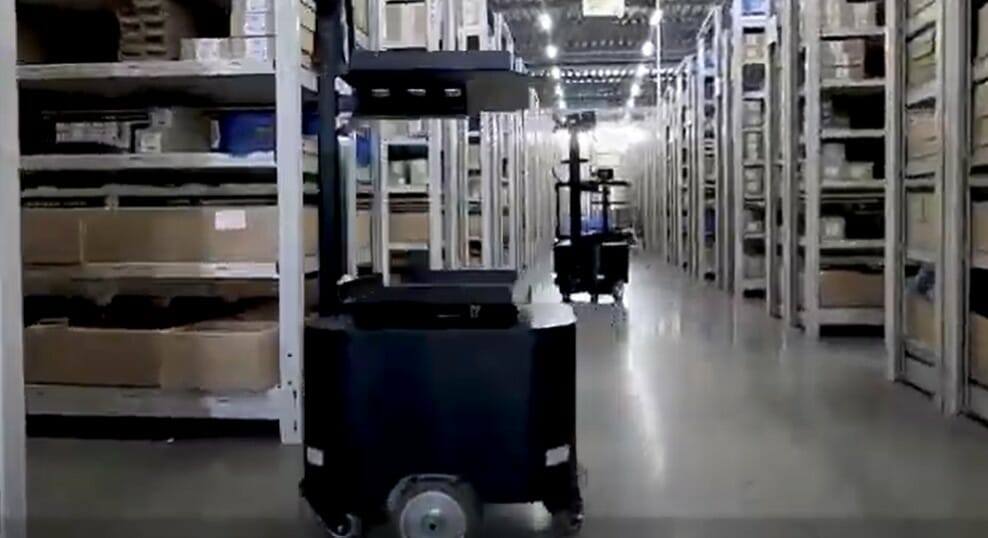
AMRを導入するには?最短4ヶ月で導入が可能!
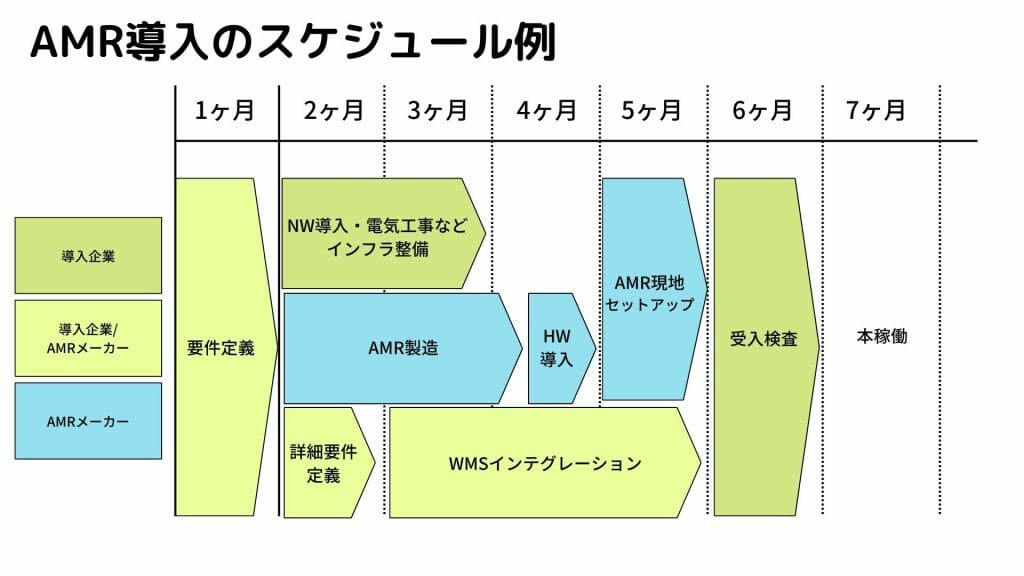
AMRの導入期間は標準で6ヶ月程度、最短では4ヶ月と他の物流ロボットを導入する場合(12ヶ月~数年程度)と比較しても大変短いです。
要件定義からインフラ設備、WMSインテグレーション、受け入れ検査に至るまでを早いスケジュール感で進めていきます。
既存のラックレイアウトを変更する必要がないため、AGV(GTP)や自動倉庫など、他の物流ロボット、物流設備に比べて短期間で導入が可能なため、現場に負担をかけずに導入することができます。またキックオフから導入までのスケジュールが短いため、投資回収期間を短縮できるのもAMRのメリットの一つです。
まとめ
今回はAMR(協働搬送ロボット)の概要や他のロボットとの比較、導入のメリット、物流改善事例、導入スケジュールについて解説いたしました。
ご参考になれば幸いです。
マテバンクではAMRメーカーのラピュタロボティクス社と業務提携を行っております。
ただいま期間限定でAMRのご紹介キャンペーンも行っておりますので、AMRの導入を検討されている事業者様はぜひ下記リンクのキャンペーンをご覧ください。
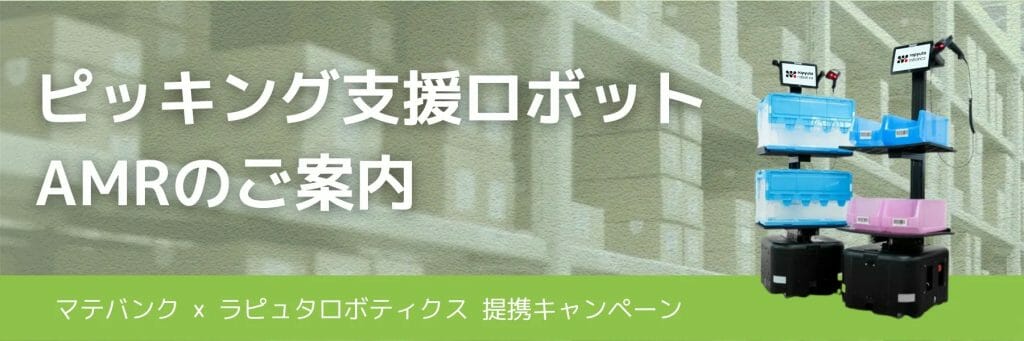